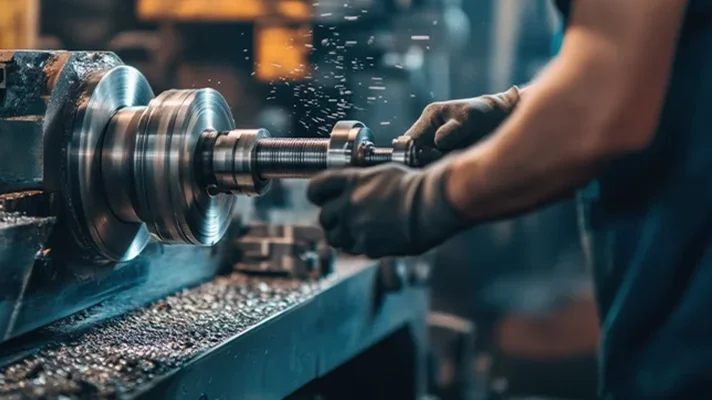
Concerns and Hazards
Metal working operations use a wide variety of equipment, from brand new items to decades old machines. But no matter what type they are, metal working machines often present similar mechanical hazards. Injuries from machine operation are typically very serious but can be prevented with proper machine safeguarding practices that cover operation and service or repair work.
Basic Machine Safeguarding Practices
Machine-related accidents from metal working equipment may be caused by:
- Being struck by metal chips or fines created by a machine.
- Contact with a lathe chuck, tooling, or devices that hold work.
- Interacting with moving parts like belt or pulleys that are not properly guarded.
- Placing a hand on rotating chucks or not removing chuck keys for manual equipment.
Using a tool in contact with moving parts.
When evaluating the safety of metal working equipment, look at the point of operation where work is performed, but also review moving parts like gears, shafts, belts, cables, and hydraulic or pneumatic cylinders.
At a minimum, machine safeguarding practices must follow OSHA 1910.212 General Requirements. Some states, like Michigan, have created their own standard and Michigan’s Part 26 Metalworking Machinery covers this topic. The standards detail requirements for point of operation, tool use, and other hazards. Fixed guards must follow OSHA table O-10 regarding guard opening sizes in relation to the distance from the hazard.
Good machine safeguarding covers more than just physical guards. It also includes other safety devices (light curtains, interlocked doors), controls (reliable), disconnects for lockout, starters (no automatic restart), and employee training.
Metal working equipment includes a wide variety of items like lathes, mills, boring machines, grinding machines, and metal saws. Manual equipment, like a bench grinder or manual lathe, moves or operates only when the employee moves a control. New equipment cycles and machines the part automatically after it is loaded by the operator. Common hazards include:
- Coolants or metal chips – these can fly off machines and cause lacerations or eye injuries.
- Flying objects – improperly secured parts that fly out of machines and strike people.
- Point of operation – part of the machine where an operator is directly interacting with the machine.
- Power transmission – belts, pulleys, and wheels that turn to power the machine or parts of it.
Following are general rules for safeguarding metal working equipment and operation:
- All machines require a chuck shield to control any chips, metal fines, and coolants that are created when operating the machine.
- For manually operated equipment, chuck keys must be spring loaded or interlocked. This reduces the risk of the key being left in the chuck, where it could fly out when the chuck starts to turn.
- Machine movement cannot be used to tighten or torque parts onto fixtures.
- Machines that operate automatically after they are programmed require point of operation safeguarding since the operator can leave the controls. This can include fixed guards or doors with interlock switches.
- Manually operated machines do not require point of operation safeguarding because the operator controls the movement of tooling to engage the part. Other safeguarding practices must still be followed.
- Operators must always wait for the machine to stop before measuring or changing parts.
- Operators must be trained to secure parts properly and operate the equipment safely.
- Operators must follow safe operation rules at all times. Personal practices include not slowing spindles by hand, wearing personal protective equipment, not wearing loose clothing or long sleeves, not wearing hoods, not wearing jewelry, and keeping hair pulled back at all times.
- Operators should never use improvised pry bars or tools to operate equipment.
Lockout/Tagout De-Energizing Equipment
Many accidents with properly guarded equipment occur during service or repair work when the machine is not properly de-energized and locked out. Every person must follow the lockout procedures to completely de-energize and secure equipment.
General requirements include:
- Survey and identify all equipment that is serviced, repaired, or requires an employee to access a hazardous area when safeguards are removed or bypassed.
- Identify all energy sources and label all energy isolation devices that turn off and isolate power. Power sources can include but are not limited to: electrical, hydraulics, air, or even gravity. Many machines have multiple energy sources, and all must be addressed.
- Write a policy that covers general rules and also machine-specific procedure for each machine. This is required because each piece of equipment typically has its own methods to de-energize and lockout. The only exception where a single procedure can be used is when multiple machines can be de-energized and locked out using the exact same procedure.
- The company must provide all locks and tags and implement a method to control keys. All locks must be key operated and combination locks cannot be used. Locks cannot be used for any purpose other than to lockout equipment.
- Train all employees and provide document training. Authorized employees include people who will actually work on equipment and follow the lockout procedure. Maintain a list of active authorized employees, who must be trained on machine-specific procedures by another authorized person. All other employees must also participate in training to have knowledge of lockout hazards. They cannot participate in a lockout procedure or attempt to operate a machine that is being serviced.
- Monitor the program with audits or inspections to verify that lockout procedures are being followed. Violations must be addressed and employees retrained where necessary.